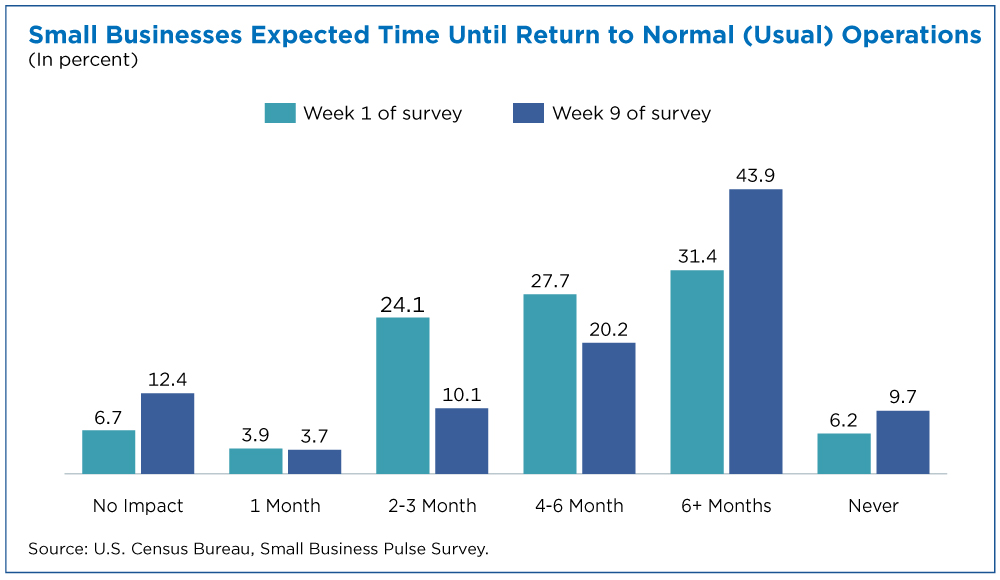
Across the industrial manufacturing industry, the Industrial Products & Services sector is facing intensified global competition, as well as a shortage of skilled workers. In 2020, the industry will face a complex landscape due to volatility in supply chains and increased competition. To ensure that growth is maximized in existing markets and to maximise growth opportunities in new markets, the Industrial Products & Services industry requires a culture of innovation.
According to the Deloitte and Manufacturing Institute study, the US manufacturing workforce will experience the largest shortfall of skilled workers in history, as 2 million jobs are estimated to be unfilled over the next decade. As the industry prepares for the future, manufacturers must decide how they will develop their digital and innovation capabilities. Deloitte's Industrial Manufacturing Team can help manufacturers navigate the landscape of the industry.
As the fourth industrial revolution continues its disruption in the manufacturing sector, the industry must prepare employees for a future that includes networking within the internet of things' as well as digital transformation. The Industrial Manufacturing team is skilled at establishing innovative management models that are grounded industry-specific expertise and deep industry knowledge. It also offers a wide range digital transformation services that can be used to assist manufacturers in the digital age.
The Deloitte study is based on extensive secondary data analysis of labor supply, as well as interviews with executives from manufacturing organizations of all sizes. The research also includes economic projections. The importance of diversity in the workforce is also highlighted by these findings. In particular, half of respondents said that adaptability to company values was key to their job happiness. Over a third of respondents said that employees need to have a purpose to feel satisfied at their jobs. Executives also think that millennials value environmental awareness and are increasingly interested in climate change issues.
Using the Oxford Economic Model, Deloitte predicts that manufacturing GDP will grow at a moderate rate of 1.3 percent in 2020. However, the study indicates that this rate of growth is likely to be less than half what it was in the past few year. This means companies will need a rethink on their supply chain assurance policies. Businesses will need to focus their efforts on other management initiatives such a greater resilience in operations. According to Deloitte, manufacturers are likely to make decisions about their workplaces and work methods.
Manufacturing companies should create opportunities for career advancement and promote inclusion in order to plan for the future. Manufacturing efficiency can be improved and waste reduced by increasing resilience. The combination of digital technology and lean principles may also reduce manufacturing variability.
As the US manufacturing industry continues to evolve, Deloitte has released a new report that explores diversity in manufacturing. Deloitte’s "Beyond Reskilling” report discusses the importance of diversity in manufacturing's future and highlights the advantages of having a diverse workforce.
FAQ
How can manufacturing reduce production bottlenecks?
The key to avoiding bottlenecks in production is to keep all processes running smoothly throughout the entire production cycle, from the time you receive an order until the time when the product ships.
This includes both planning for capacity and quality control.
Continuous improvement techniques such Six Sigma are the best method to accomplish this.
Six Sigma is a management system used to improve quality and reduce waste in every aspect of your organization.
It is focused on creating consistency and eliminating variation in your work.
What are manufacturing and logistic?
Manufacturing refers to the process of making goods using raw materials and machines. Logistics manages all aspects of the supply chain, including procurement, production planning and distribution, inventory control, transportation, customer service, and transport. As a broad term, manufacturing and logistics often refer to both the creation and delivery of products.
How can manufacturing excess production be decreased?
Better inventory management is key to reducing excess production. This would reduce the time spent on unproductive activities like purchasing, storing and maintaining excess stock. By doing this, we could free up resources for other productive tasks.
Kanban systems are one way to achieve this. A Kanban board is a visual display used to track work in progress. A Kanban system allows work items to move through several states before reaching their final destination. Each state represents a different priority.
To illustrate, work can move from one stage or another when it is complete enough for it to be moved to a new stage. A task that is still in the initial stages of a process will be considered complete until it moves on to the next stage.
This allows work to move forward and ensures that no work is missed. With a Kanban board, managers can see exactly how much work is being done at any given moment. This information allows managers to adjust their workflow based off real-time data.
Lean manufacturing is another way to manage inventory levels. Lean manufacturing emphasizes eliminating waste in all phases of production. Any product that isn't adding value can be considered waste. The following are examples of common waste types:
-
Overproduction
-
Inventory
-
Packaging that is not necessary
-
Excess materials
These ideas can help manufacturers improve efficiency and reduce costs.
What is the job of a manufacturer manager?
Manufacturing managers must ensure that manufacturing processes are efficient, effective, and cost-effective. They should be alert for any potential problems in the company and react accordingly.
They should also be able communicate with other departments, such as sales or marketing.
They should be informed about industry trends and be able make use of this information to improve their productivity and efficiency.
Statistics
- According to the United Nations Industrial Development Organization (UNIDO), China is the top manufacturer worldwide by 2019 output, producing 28.7% of the total global manufacturing output, followed by the United States, Japan, Germany, and India.[52][53] (en.wikipedia.org)
- It's estimated that 10.8% of the U.S. GDP in 2020 was contributed to manufacturing. (investopedia.com)
- In 2021, an estimated 12.1 million Americans work in the manufacturing sector.6 (investopedia.com)
- You can multiply the result by 100 to get the total percent of monthly overhead. (investopedia.com)
- In the United States, for example, manufacturing makes up 15% of the economic output. (twi-global.com)
External Links
How To
How to use lean manufacturing in the production of goods
Lean manufacturing (or lean manufacturing) is a style of management that aims to increase efficiency, reduce waste and improve performance through continuous improvement. It was created in Japan by Taiichi Ohno during the 1970s and 80s. He received the Toyota Production System award (TPS), from Kanji Toyoda, founder of TPS. Michael L. Watkins published the book "The Machine That Changed the World", which was the first to be published about lean manufacturing.
Lean manufacturing refers to a set of principles that improve the quality, speed and costs of products and services. It emphasizes the elimination and minimization of waste in the value stream. The five-steps of Lean Manufacturing are just-in time (JIT), zero defect and total productive maintenance (TPM), as well as 5S. Lean manufacturing seeks to eliminate non-value added activities, such as inspection, work, waiting, and rework.
Lean manufacturing not only improves product quality but also reduces costs. Companies can also achieve their goals faster by reducing employee turnover. Lean Manufacturing is one of the most efficient ways to manage the entire value chains, including suppliers and customers as well distributors and retailers. Lean manufacturing is widely used in many industries. For example, Toyota's philosophy underpins its success in automobiles, electronics, appliances, healthcare, chemical engineering, aerospace, paper, food, etc.
Lean manufacturing includes five basic principles:
-
Define Value: Identify the social value of your business and what sets you apart.
-
Reduce Waste – Eliminate all activities that don't add value throughout the supply chain.
-
Create Flow: Ensure that the work process flows without interruptions.
-
Standardize and simplify - Make your processes as consistent as possible.
-
Build relationships - Develop and maintain personal relationships with both your internal and external stakeholders.
Although lean manufacturing isn't a new concept in business, it has gained popularity due to renewed interest in the economy after the 2008 global financial crisis. Many companies have adopted lean manufacturing methods to increase their marketability. Many economists believe lean manufacturing will play a major role in economic recovery.
Lean manufacturing is now becoming a common practice in the automotive industry, with many benefits. These include improved customer satisfaction, reduced inventory levels, lower operating costs, increased productivity, and better overall safety.
It can be applied to any aspect of an organisation. Lean manufacturing is most useful in the production sector of an organisation because it ensures that each step in the value-chain is efficient and productive.
There are three main types of lean manufacturing:
-
Just-in Time Manufacturing: This lean manufacturing method is commonly called "pull systems." JIT stands for a system where components are assembled on the spot rather than being made in advance. This strategy aims to decrease lead times, increase availability of parts and reduce inventory.
-
Zero Defects Manufacturing, (ZDM): ZDM is focused on ensuring that no defective products leave the manufacturing facility. You should repair any part that needs to be repaired during an assembly line. This applies to finished products, which may need minor repairs before they are shipped.
-
Continuous Improvement (CI),: Continuous improvement aims improve the efficiency and effectiveness of operations by continuously identifying issues and making changes to reduce waste. Continuous improvement involves continuous improvement of processes and people as well as tools.