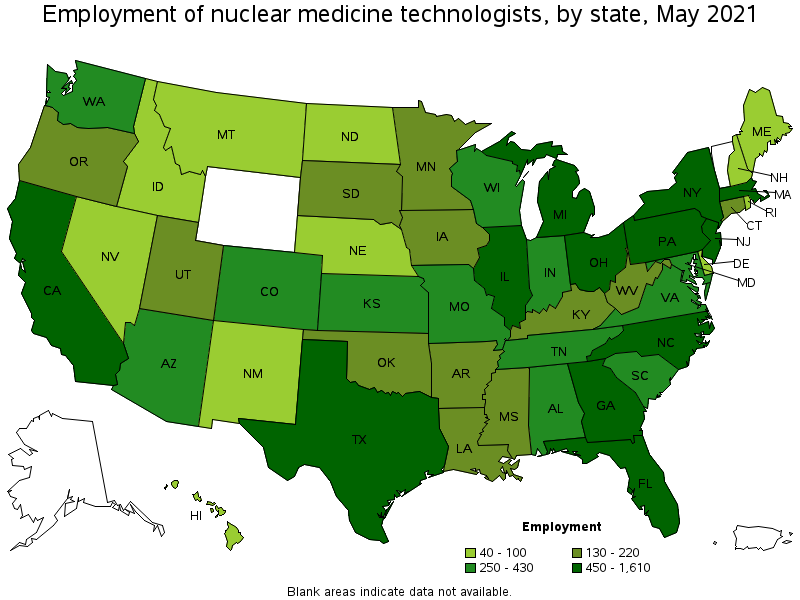
What role does an environmentalist play in mining
Engineers play a vital role in the mining industry. They are responsible for gathering, refining and transporting raw materials, which we use daily. They design systems for mining and refining that are profitable for the companies which mine and refine the materials.
How much money does a mine engineer make?
Salary is determined by many factors such as company and job. A mining engineer's salary can start at PS22,000, but can increase to PS50,000 with experience. Senior engineers are able to earn PS80,000 per annum or even more.
What are the subjects that make up mining engineering?
To be a mining engineering, you need to have an understanding of several disciplines. These include electrical, mechanical, geological, and civil engineering. They should be able design and operate mining equipment, manage mine operations and provide technical assistance to other engineers.
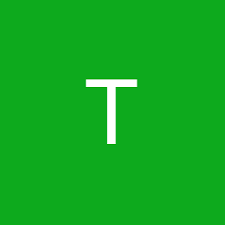
How to find a job as a mining engineering?
The first step in getting a career as a mining engineer is to earn a degree and gain work experience. This will give you the chance to show off your skills and demonstrate to prospective employers that you have the right attitude and qualifications. You may also be able to find a job with a firm that specializes in mining engineering. This will give you the opportunity to use your expertise and knowledge.
How to find mining engineer jobs
Most mining engineering jobs can be found overseas. However, there are a few opportunities in the UK. These are usually at large international companies. Most of these jobs require working on-site for extended periods of time and traveling to other parts around the world.
How to choose a career in mining engineering
A career as a mining engineering is not only challenging but also offers many opportunities for growth and development. You can work your way up to become a lead or senior engineer, and then take on further managerial and strategic responsibilities.
How to prepare yourself for a job as a mining engineer
The requirements for a career as a mining engineer include a university degree and relevant work experience. Graduates can often start their careers as trainee engineers, working with a mentor and learning from experienced professionals. This provides an excellent opportunity to develop your skills and build a network of contacts.
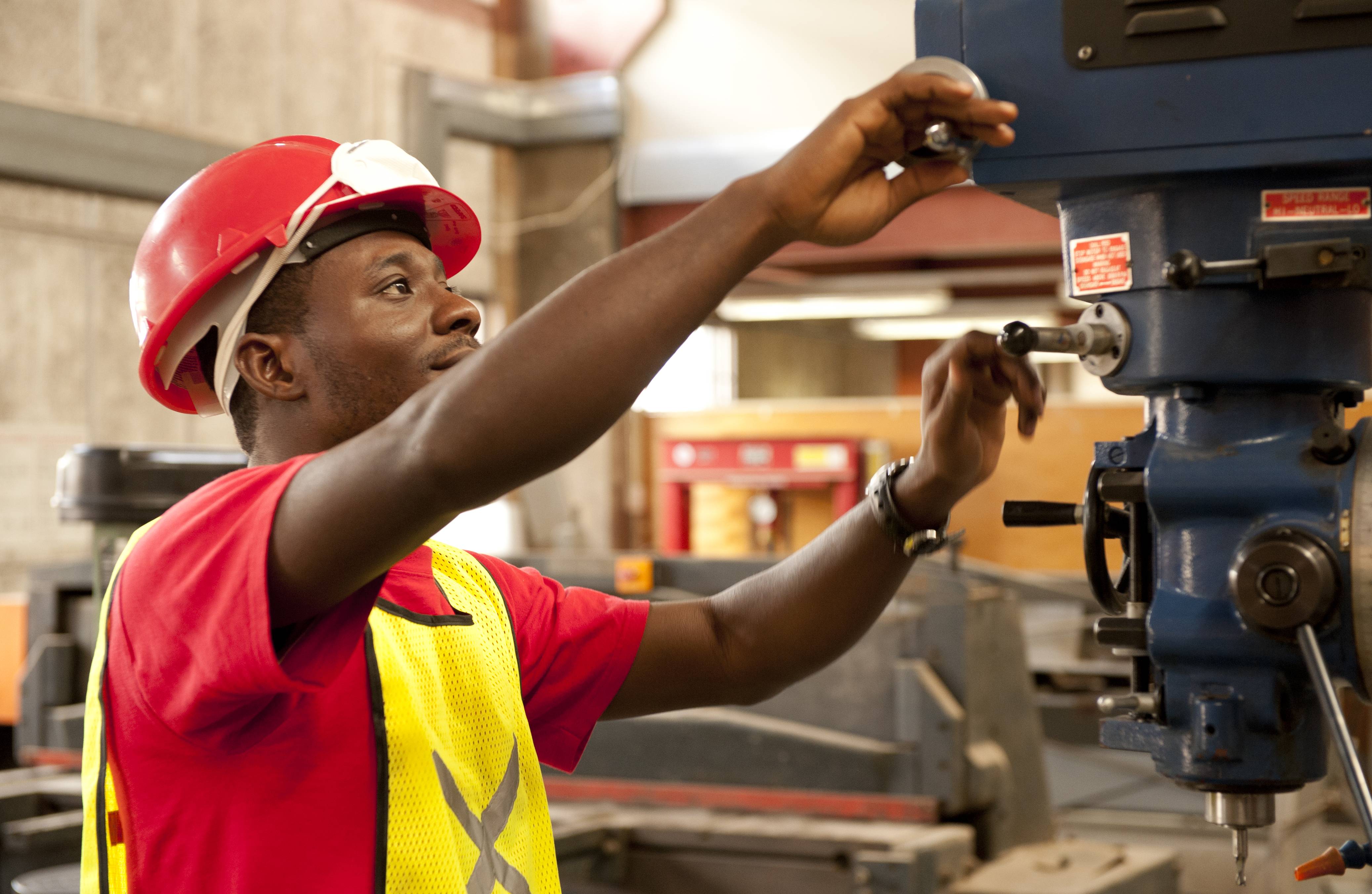
How to search for a mining job
These companies are the best places to find jobs in the mining engineering field. You can find vacancies with these firms online, by specialist recruitment agencies and in publications such as targetjobs Engineering, Mining Journal, and InfoMine. Search for speculative positions in the Directory of Mines and Quarries by the British Geological Survey.
How to become a mining engineer
A career in mining can be started by obtaining a degree or master's in geology, and then gaining experience in the industry. If you're particularly interested in this subject, you can consider a PhD or a master's program.
FAQ
Can certain manufacturing steps be automated?
Yes! Yes! Automation has existed since ancient times. The Egyptians invented the wheel thousands of years ago. Today, robots assist in the assembly of lines.
There are many applications for robotics in manufacturing today. These include:
-
Line robots
-
Robot welding
-
Robot painting
-
Robotics inspection
-
Robots that create products
Manufacturing could also benefit from automation in other ways. 3D printing makes it possible to produce custom products in a matter of days or weeks.
What are the 7 Rs of logistics management?
The acronym 7Rs of Logistics refers to the seven core principles of logistics management. It was created by the International Association of Business Logisticians and published in 2004 under its "Seven Principles of Logistics Management".
The following letters form the acronym:
-
Responsible - ensure that all actions taken are within legal requirements and are not harmful to others.
-
Reliable – have faith in your ability and capability to keep promises.
-
Be responsible - Use resources efficiently and avoid wasting them.
-
Realistic - Consider all aspects of operations, including environmental impact and cost effectiveness.
-
Respectful - treat people fairly and equitably.
-
Reliable - Find ways to save money and increase your productivity.
-
Recognizable - provide customers with value-added services.
What are the logistics products?
Logistics are the activities involved in moving goods from point A to point B.
These include all aspects related to transport such as packaging, loading and transporting, storing, transporting, unloading and warehousing inventory management, customer service. Distribution, returns, recycling are some of the options.
Logisticians ensure that the product is delivered to the correct place, at the right time, and under safe conditions. They provide information on demand forecasts as well stock levels, production schedules and availability of raw material.
They coordinate with vendors and suppliers, keep track of shipments, monitor quality standards and perform inventory and order replenishment.
What is the job of a production plan?
Production planners ensure all aspects of the project are delivered within time and budget. They make sure that the product and services meet client expectations.
Statistics
- In 2021, an estimated 12.1 million Americans work in the manufacturing sector.6 (investopedia.com)
- According to the United Nations Industrial Development Organization (UNIDO), China is the top manufacturer worldwide by 2019 output, producing 28.7% of the total global manufacturing output, followed by the United States, Japan, Germany, and India.[52][53] (en.wikipedia.org)
- Many factories witnessed a 30% increase in output due to the shift to electric motors. (en.wikipedia.org)
- You can multiply the result by 100 to get the total percent of monthly overhead. (investopedia.com)
- In the United States, for example, manufacturing makes up 15% of the economic output. (twi-global.com)
External Links
How To
How to use the Just-In Time Method in Production
Just-intime (JIT), a method used to lower costs and improve efficiency in business processes, is called just-in-time. It's a way to ensure that you get the right resources at just the right time. This means you only pay what you use. Frederick Taylor, a 1900s foreman, first coined the term. Taylor observed that overtime was paid to workers if they were late in working. He decided to ensure workers have enough time to do their jobs before starting work to improve productivity.
JIT is an acronym that means you need to plan ahead so you don’t waste your money. Also, you should look at the whole project from start-to-finish and make sure you have the resources necessary to address any issues. You'll be prepared to handle any potential problems if you know in advance. This way, you won't end up paying extra money for things that weren't really necessary.
There are different types of JIT methods:
-
Demand-driven: This JIT is where you place regular orders for the parts/materials that are needed for your project. This will enable you to keep track of how much material is left after you use it. You'll also be able to estimate how long it will take to produce more.
-
Inventory-based : You can stock the materials you need in advance. This allows one to predict how much they will sell.
-
Project-driven: This is an approach where you set aside enough funds to cover the cost of your project. When you know how much you need, you'll purchase the appropriate amount of materials.
-
Resource-based JIT: This type of JIT is most commonly used. Here, you allocate certain resources based on demand. If you have many orders, you will assign more people to manage them. If you don't have many orders, you'll assign fewer people to handle the workload.
-
Cost-based: This approach is very similar to resource-based. However, you don't just care about the number of people you have; you also need to consider how much each person will cost.
-
Price-based: This is very similar to cost-based, except that instead of looking at how much each individual worker costs, you look at the overall price of the company.
-
Material-based - This is a variant of cost-based. But instead of looking at the total company cost, you focus on how much raw material you spend per year.
-
Time-based: This is another variation of resource-based JIT. Instead of focusing solely on the amount each employee costs, focus on how long it takes for the project to be completed.
-
Quality-based JIT is another variant of resource-based JIT. Instead of thinking about the cost of each employee or the time it takes to produce something, you focus on how good your product quality.
-
Value-based JIT : This is the newest type of JIT. In this instance, you are not concerned about the product's performance or meeting customer expectations. Instead, you focus on the added value that you provide to your market.
-
Stock-based is an inventory-based system that measures the number of items produced at any given moment. It's useful when you want maximum production and minimal inventory.
-
Just-in-time (JIT) planning: This is a combination of JIT and supply chain management. It is the process of scheduling components' delivery as soon as they have been ordered. It's important because it reduces lead times and increases throughput.