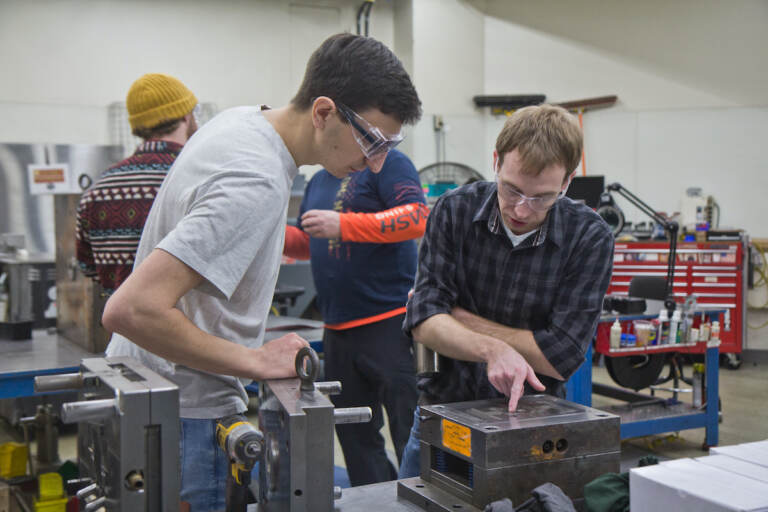
You're here because you are interested in a salary in biochemistry. This article will provide information on biochemical salaries for BOTHELL, WA, and San Mateo CA. Explore the various biochemical salaries options to get started in your career. Find out more about the requirements for salary and job descriptions at Worthington Biochemical as well as Youtell Biochemical. Both companies are located in BOTHELL WA and offer competitive benefits as well as compensation.
Youtell Biochemical's hourly salary is $29
Youtell Biochemical's average salary is $99,854. Salary ranges from $88,159 - $114,509. The individual salary can vary depending on the position and education as well as the skills required. Here are some examples for the types and salaries at Youtell Biochemical. The salary ranges are also based on experience and education, so keep this in mind when evaluating salaries.
Youtell Biochemical's headquarters is located in BOTHELL WA
Youtell Biochemical is a chemical firm based in BOTHELL WA that specializes in enzyme products. They have a stateof-the-art biotechnology center in Bothell, as well two downstream processing plants and fermentation factories located in China. The enzyme products are produced by these companies using patented technologies. Youtell Biochemical produces over 80,000 tons per year of enzyme products at its main campus in BOTHELL WA.
Worthington Biochemical is based in San Mateo, CA
Worthington Biochemical started in 1947. Its founder, Charles Worthington, had worked as a research assistant at the Rockefeller Institute, preparing crystalline enzymes for use in biochemical research. He quickly realized that the growing biochemical research community was in need of reliable, high-purity enzymes, and that researchers would have to spend a lot of time purifying them themselves. Worthington started his own company in 1947, in Freehold, New Jersey, to supply these enzymes.
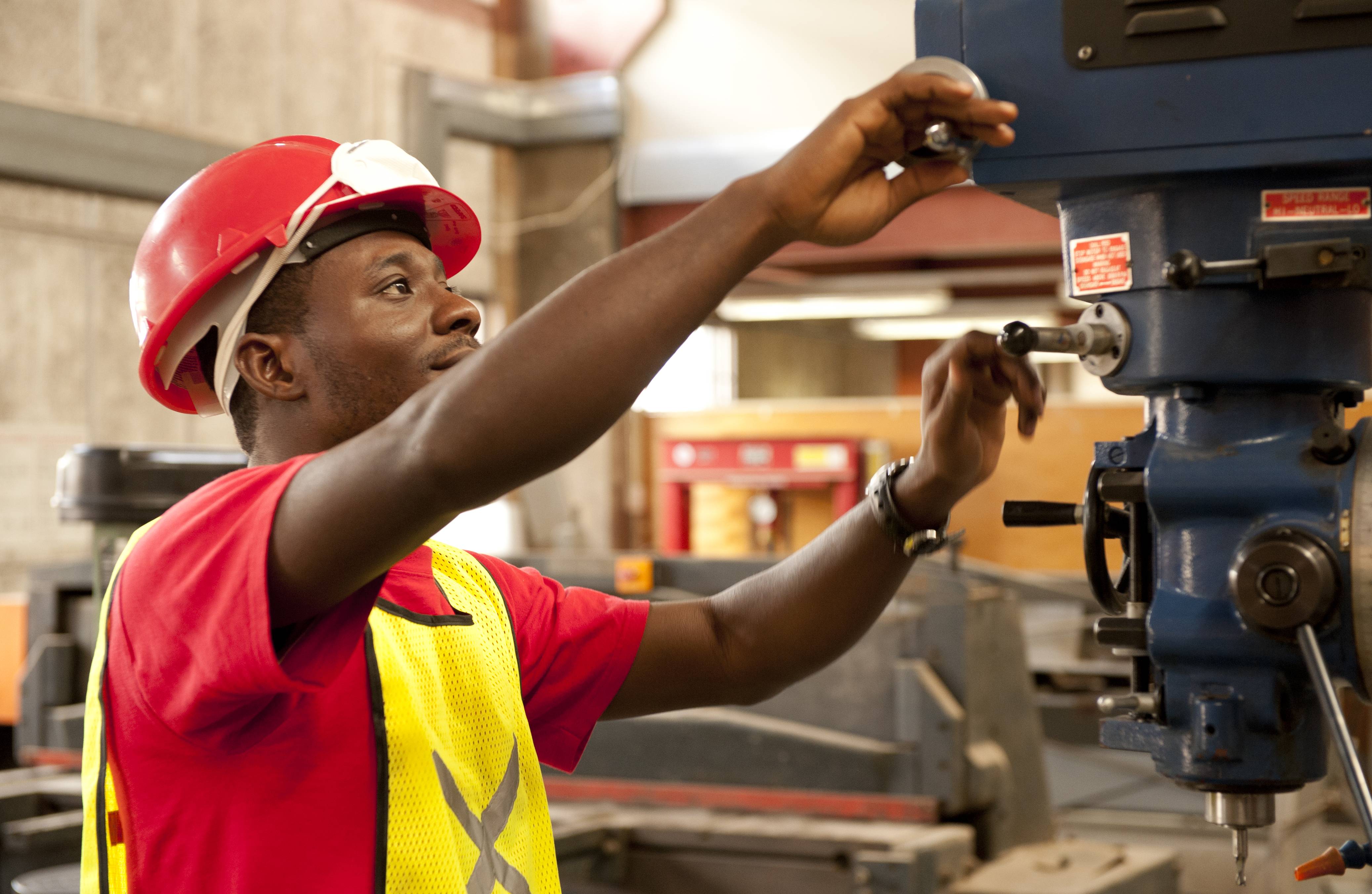
In 1985, Worthington acquired the Clinical Division of Cooper, a biotech firm based in New Jersey. Worthington was able to expand its operations while still focusing on the lucrative clinical market. However, the company failed to expand into the fields of molecular biology and immunology. Instead, it expanded its diagnostic kit manufacturing facility while investing less in enzyme production.
FAQ
How can excess manufacturing production be reduced?
Better inventory management is key to reducing excess production. This would reduce the time spent on unproductive activities like purchasing, storing and maintaining excess stock. This would allow us to use our resources for more productive tasks.
Kanban systems are one way to achieve this. A Kanban board can be used to monitor work progress. In a Kanban system, work items move through a sequence of states until they reach their final destination. Each state represents a different priority.
As an example, if work is progressing from one stage of the process to another, then the current task is complete and can be transferred to the next. If a task is still in its beginning stages, it will continue to be so until it reaches the end.
This allows for work to continue moving forward, while also ensuring that there is no work left behind. A Kanban board allows managers to monitor how much work is being completed at any given moment. This information allows them to adjust their workflow based on real-time data.
Lean manufacturing is another way to manage inventory levels. Lean manufacturing emphasizes eliminating waste in all phases of production. Anything that does not contribute to the product's value is considered waste. There are several types of waste that you might encounter:
-
Overproduction
-
Inventory
-
Packaging not required
-
Overstock materials
These ideas can help manufacturers improve efficiency and reduce costs.
How can manufacturing reduce production bottlenecks?
Avoiding production bottlenecks is as simple as keeping all processes running smoothly, from the time an order is received until the product ships.
This includes both quality control and capacity planning.
This can be done by using continuous improvement techniques, such as Six Sigma.
Six Sigma management is a system that improves quality and reduces waste within your organization.
It emphasizes consistency and eliminating variance in your work.
Is it possible to automate certain parts of manufacturing
Yes! Yes. The Egyptians discovered the wheel thousands and years ago. Today, robots assist in the assembly of lines.
Actually, robotics can be used in manufacturing for many purposes. These include:
-
Assembly line robots
-
Robot welding
-
Robot painting
-
Robotics inspection
-
Robots that create products
Manufacturing could also benefit from automation in other ways. For example, 3D printing allows us to make custom products without having to wait for weeks or months to get them manufactured.
Why automate your warehouse
Modern warehouses are increasingly dependent on automation. E-commerce has brought increased demand for more efficient and quicker delivery times.
Warehouses must adapt quickly to meet changing customer needs. Technology is essential for warehouses to be able to adapt quickly to changing needs. Automating warehouses has many benefits. Here are some reasons why it's worth investing in automation:
-
Increases throughput/productivity
-
Reduces errors
-
Accuracy is improved
-
Safety Boosts
-
Eliminates bottlenecks
-
Companies can scale more easily
-
This makes workers more productive
-
This gives you visibility into what happens in the warehouse
-
Enhances customer experience
-
Improves employee satisfaction
-
Reducing downtime and increasing uptime
-
This ensures that quality products are delivered promptly
-
Eliminates human error
-
It helps ensure compliance with regulations
What is the role of a manager in manufacturing?
A manufacturing manager must ensure that all manufacturing processes are efficient and effective. They must also be alert to any potential problems and take appropriate action.
They should also be able communicate with other departments, such as sales or marketing.
They should also be knowledgeable about the latest trends in the industry so they can use this information for productivity and efficiency improvements.
What does warehouse mean?
A warehouse, or storage facility, is where goods are stored prior to being sold. It can be indoors or out. In some cases it could be both indoors and outdoors.
What type of jobs is there in logistics
There are many jobs available in logistics. Some examples are:
-
Warehouse workers: They load and unload trucks, pallets, and other cargo.
-
Transportation drivers: They drive trucks and trailers and deliver goods and make pick-ups.
-
Freight handlers – They sort and package freight at warehouses.
-
Inventory managers: They are responsible for the inventory and management of warehouses.
-
Sales representatives - They sell products.
-
Logistics coordinators - They plan and organize logistics operations.
-
Purchasing agents are those who purchase goods and services for the company.
-
Customer service representatives are available to answer customer calls and emails.
-
Shipping clerks: They process shipping requests and issue bills.
-
Order fillers – They fill orders based upon what was ordered and shipped.
-
Quality control inspectors – They inspect incoming and outgoing products to ensure that there are no defects.
-
Others - There are many types of jobs in logistics such as transport supervisors and cargo specialists.
Statistics
- In the United States, for example, manufacturing makes up 15% of the economic output. (twi-global.com)
- You can multiply the result by 100 to get the total percent of monthly overhead. (investopedia.com)
- (2:04) MTO is a production technique wherein products are customized according to customer specifications, and production only starts after an order is received. (oracle.com)
- Many factories witnessed a 30% increase in output due to the shift to electric motors. (en.wikipedia.org)
- [54][55] These are the top 50 countries by the total value of manufacturing output in US dollars for its noted year according to World Bank.[56] (en.wikipedia.org)
External Links
How To
How to use the Just-In Time Method in Production
Just-intime (JIT), a method used to lower costs and improve efficiency in business processes, is called just-in-time. This is where you have the right resources at the right time. This means that your only pay for the resources you actually use. The term was first coined by Frederick Taylor, who developed his theory while working as a foreman in the early 1900s. Taylor observed that overtime was paid to workers if they were late in working. He decided to ensure workers have enough time to do their jobs before starting work to improve productivity.
The idea behind JIT is that you should plan ahead and have everything ready so you don't waste money. Look at your entire project, from start to end. Make sure you have enough resources in place to deal with any unexpected problems. If you anticipate that there might be problems, you'll have enough people and equipment to fix them. This will ensure that you don't spend more money on things that aren't necessary.
There are many JIT methods.
-
Demand-driven: This is a type of JIT where you order the parts/materials needed for your project regularly. This will enable you to keep track of how much material is left after you use it. You'll also be able to estimate how long it will take to produce more.
-
Inventory-based: This allows you to store the materials necessary for your projects in advance. This allows you predict the amount you can expect to sell.
-
Project-driven: This means that you have enough money to pay for your project. You will be able to purchase the right amount of materials if you know what you need.
-
Resource-based JIT is the most widespread form. Here you can allocate certain resources based purely on demand. For instance, if you have a lot of orders coming in, you'll assign more people to handle them. You'll have fewer orders if you have fewer.
-
Cost-based: This is the same as resource-based except that you don't care how many people there are but how much each one of them costs.
-
Price-based pricing: This is similar in concept to cost-based but instead you look at how much each worker costs, it looks at the overall company's price.
-
Material-based: This approach is similar to cost-based. However, instead of looking at the total cost for the company, you look at how much you spend on average on raw materials.
-
Time-based JIT: This is another variant of resource-based JIT. Instead of worrying about how much each worker costs, you can focus on how long the project takes.
-
Quality-based JIT: Another variation on resource-based JIT. Instead of looking at the labor costs and time it takes to make a product, think about its quality.
-
Value-based: This is one of the newest forms of JIT. You don't worry about whether the products work or if they meet customer expectations. Instead, your goal is to add value to the market.
-
Stock-based is an inventory-based system that measures the number of items produced at any given moment. This is used to increase production and minimize inventory.
-
Just-in-time (JIT) planning: This is a combination of JIT and supply chain management. It is the process of scheduling components' delivery as soon as they have been ordered. It's important because it reduces lead times and increases throughput.