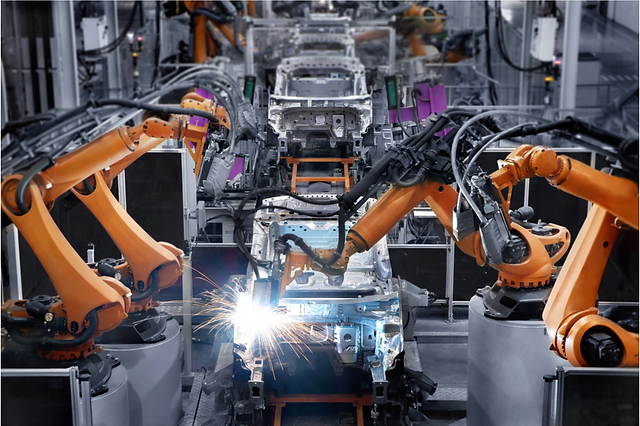
Denver is a city in Colorado that offers a wide variety of jobs. It also has several logistics companies which offer a variety of logistics services. Some of these services include freight-forwarding, trucking, logistics and supply chain consultancy, as well.
If you're interested in a career in logistics, you may want to consider a number of different positions, such as dispatcher, transportation director and warehouse assistant. All of these positions have the responsibility of ensuring that logistics are run smoothly in an organization.
Dispatch manager
A dispatch manager's job is to coordinate and direct the activities of teams that work in a store or call center. This includes training new employees, delegating tasks, coordinating the workload of other team members, documenting productivity, and overseeing incoming and outgoing shipments. Dispatch managers usually have a bachelor's degree in business management or logistics and experience with workflow organization.
Transportation Director
A transportation supervisor is responsible for managing the logistics within a company, school, government agency, etc. It involves establishing distribution routes and arranging transportation methods, such as buses or trucks to transport goods from one place to another.
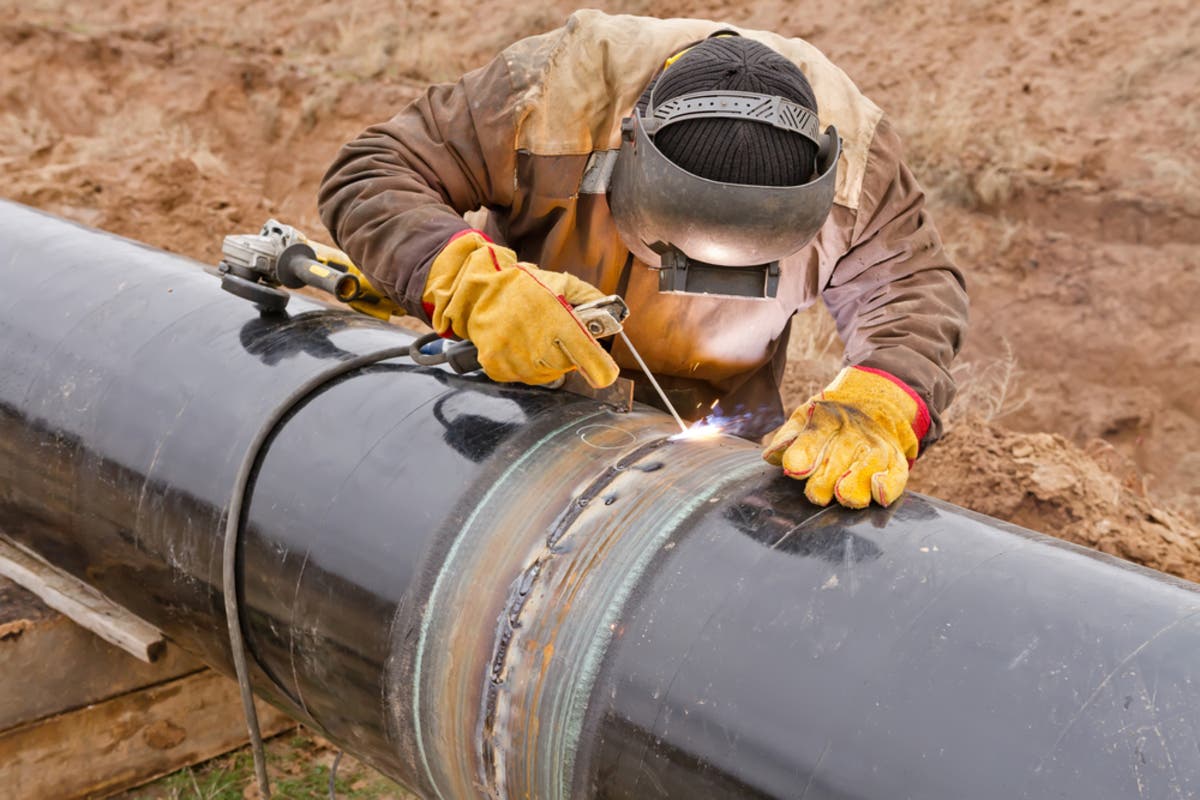
This career is suited to those who want to work for a larger company or government agency. It's a competitive job so you need to be organized and willing to work long.
Warehouse Associate
If you are looking for a job that is not as competitive, but offers a more flexible schedule, consider a warehouse associate. A warehouse associate typically handles smaller projects such as picking shipments, packing products, and moving merchandise to other locations.
Create a Monster account to begin your search for a logistics job. It will enable you to receive notifications about the latest logistics jobs in your locality.
In addition, we will provide you with expert advice regarding how to get the best out of your application for a job, how to bargain your salary and much more.
Logistics Manager
A bachelor's in supply management or business administration is required to become a manager of logistics. You need at least a year of professional experience in a warehouse environment, and you should have strong organizational skills. For a career as a senior logistics director, you may also need a master's in supply chain or a related field.
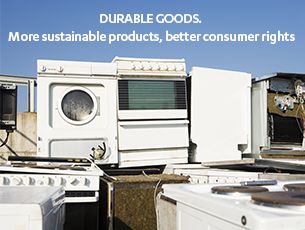
Logistik Analyst
A logistic analyst monitors the logistics of a company and works to make changes that will help the company better meet its goals. This includes evaluating the inventory levels, scheduling deliveries, and determining budget restrictions. A logistics analyst should have a Bachelor's degree in engineering or business and experience with logistics for a particular industry.
The logistics sector is expanding and offers many opportunities. You can create a free Monster account to get started in this career. You'll have the best chances to find the logistics jobs that are right for you if you create a free account on Monster.
FAQ
What kind of jobs are there in logistics?
There are many kinds of jobs available within logistics. Some examples are:
-
Warehouse workers - They load and unload trucks and pallets.
-
Transportation drivers – They drive trucks or trailers to transport goods and perform pick-ups.
-
Freight handlers – They sort and package freight at warehouses.
-
Inventory managers - These are responsible for overseeing the stock of goods in warehouses.
-
Sales reps - They sell products and services to customers.
-
Logistics coordinators - They plan and organize logistics operations.
-
Purchasing agents - They buy goods and services that are necessary for company operations.
-
Customer service representatives - They answer calls and emails from customers.
-
Shipping clerks – They process shipping orders, and issue bills.
-
Order fillers - These people fill orders based on what has been ordered.
-
Quality control inspectors – They inspect incoming and outgoing products to ensure that there are no defects.
-
Others - There are many other types of jobs available in logistics, such as transportation supervisors, cargo specialists, etc.
Why should you automate your warehouse?
Modern warehouses are increasingly dependent on automation. The rise of e-commerce has led to increased demand for faster delivery times and more efficient processes.
Warehouses should be able adapt quickly to new needs. To do so, they must invest heavily in technology. Automating warehouses has many benefits. These are just a few reasons to invest in automation.
-
Increases throughput/productivity
-
Reduces errors
-
Increases accuracy
-
Boosts safety
-
Eliminates bottlenecks
-
Allows companies to scale more easily
-
This makes workers more productive
-
Provides visibility into everything that happens in the warehouse
-
Enhances customer experience
-
Improves employee satisfaction
-
Minimizes downtime and increases uptime
-
High quality products delivered on-time
-
Human error can be eliminated
-
It helps ensure compliance with regulations
How can efficiency in manufacturing be improved?
First, we need to identify which factors are most critical in affecting production times. We then need to figure out how to improve these variables. If you don’t know how to start, look at which factors have the greatest impact upon production time. Once you've identified them, try to find solutions for each of those factors.
What are the 7 Rs of logistics?
The 7R's of Logistics is an acronym for the seven basic principles of logistics management. It was developed by International Association of Business Logisticians (IABL), and published as part of their "Seven Principles of Logistics Management Series" in 2004.
The acronym is made up of the following letters:
-
Responsible - ensure that actions are in compliance with legal requirements and do not cause harm to others.
-
Reliable - Have confidence in your ability to fulfill all of your commitments.
-
Reasonable - make sure you use your resources well and don't waste them.
-
Realistic – Consider all aspects, including cost-effectiveness as well as environmental impact.
-
Respectful - Treat people fairly and equitably
-
Responsive - Look for ways to save time and increase productivity.
-
Recognizable: Provide customers with value-added service
What is meant by manufacturing industries?
Manufacturing Industries are businesses that produce products for sale. The people who buy these products are called consumers. To accomplish this goal, these companies employ a range of processes including distribution, sales, management, and production. They make goods from raw materials with machines and other equipment. This includes all types and varieties of manufactured goods, such as food items, clothings, building supplies, furnitures, toys, electronics tools, machinery vehicles, pharmaceuticals medical devices, chemicals, among others.
Statistics
- It's estimated that 10.8% of the U.S. GDP in 2020 was contributed to manufacturing. (investopedia.com)
- (2:04) MTO is a production technique wherein products are customized according to customer specifications, and production only starts after an order is received. (oracle.com)
- According to a Statista study, U.S. businesses spent $1.63 trillion on logistics in 2019, moving goods from origin to end user through various supply chain network segments. (netsuite.com)
- [54][55] These are the top 50 countries by the total value of manufacturing output in US dollars for its noted year according to World Bank.[56] (en.wikipedia.org)
- You can multiply the result by 100 to get the total percent of monthly overhead. (investopedia.com)
External Links
How To
How to use 5S in Manufacturing to Increase Productivity
5S stands for "Sort", 'Set In Order", 'Standardize', & Separate>. Toyota Motor Corporation created the 5S methodology in 1954. It improves the work environment and helps companies to achieve greater efficiency.
This method aims to standardize production processes so that they are repeatable, measurable and predictable. This means that tasks such as cleaning, sorting, storing, packing, and labeling are performed daily. These actions allow workers to perform their job more efficiently, knowing what to expect.
There are five steps that you need to follow in order to implement 5S. Each step requires a different action, which increases efficiency. For example, when you sort things, you make them easy to find later. You arrange items by placing them in an order. Once you have separated your inventory into groups and organized them, you will store these groups in easily accessible containers. Labeling your containers will ensure that everything is correctly labeled.
This process requires employees to think critically about how they do their job. Employees need to understand the reasons they do certain jobs and determine if there is a better way. They will need to develop new skills and techniques in order for the 5S system to be implemented.
The 5S method not only increases efficiency but also boosts morale and teamwork. Once they start to notice improvements, they are motivated to keep working towards their goal of increasing efficiency.