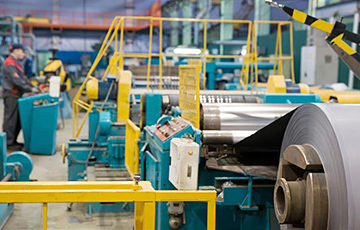
Toyota has not lost sight of its main goal to produce high-quality products, despite its successes. Toyota has achieved a reputation for being a global leader in automotive manufacturing because of its commitment to excellence.
Toyota's strategy centers on staying true and focused on incremental innovations. It also promotes smart growth. It also emphasizes how important it is to build and nurture relationships with its dealers. While other companies may choose to rely on their stock price, Toyota makes its customers the priority. Because the automobile industry is competitive, innovation is key to success.
In order to maintain its success, Toyota employees have to grapple with challenges. Toyota encourages employees in this area to explore and create new ideas. Employees are encouraged to communicate openly and challenged to make compromises and transcend differences. This can be achieved by on-thejob training. Employees are encouraged and supported to speak out about their problems and make mistakes.
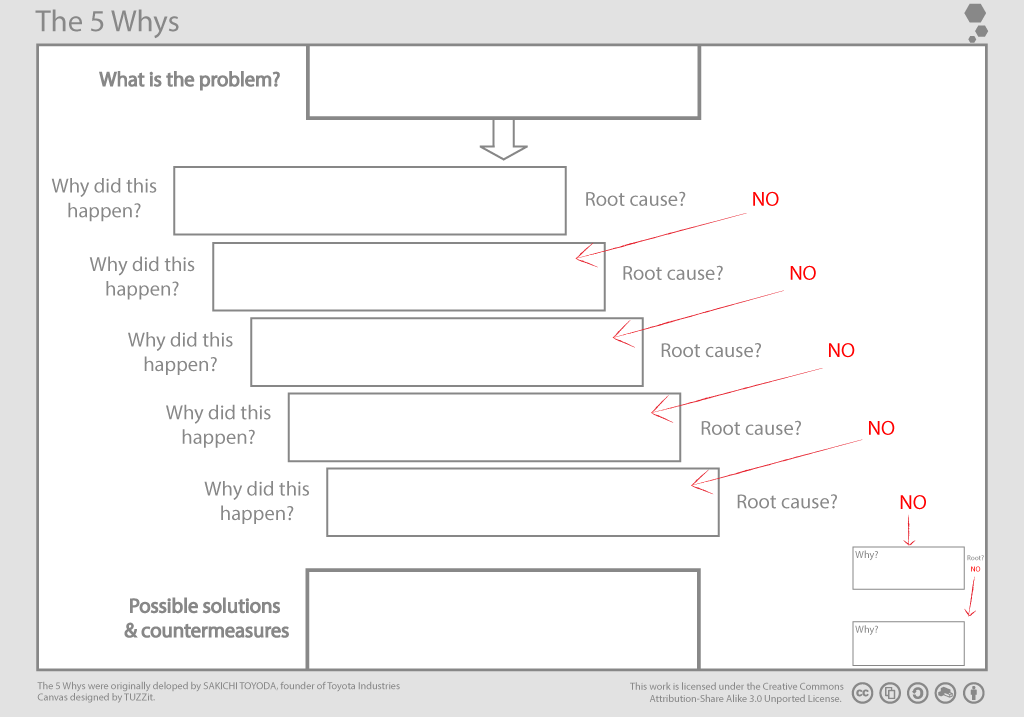
Toyota's success is also possible through continuous improvement (kaizen). The process involves streamlining processes and testing new ideas. This is known as genchi-genbutsu in Japanese. It helps Toyota reach its goals. It is also an integral part Toyota's culture. It has been the cornerstone of Toyota’s success for decades.
One of the first major moves that Toyota made was to establish a research lab. Its founder, Kiichiro Toyoda, believed that if the automobile industry was to remain competitive, it would need to develop new technologies from scratch. He set up a research lab in the late 1930s. He had a vision of a Japan producing its own automobiles and using Japanese technology.
Toyota made many strategic moves during the 1950s. It started diversifying its product line and exporting cars all over the globe. It also set up a separate sales firm and established a network dealers. It began to learn about the international auto market. It saw that American and European automakers would outnumber Toyota if Toyota wanted to compete in global markets.
Another major move that Toyota made in the '50s was to launch its own American division. Because it saw that American workers were nine-times more productive than Japanese workers, the company made this move. It realized that the market demanded fuel-efficient cars. It had to convince Americans that Japanese cars were worth the investment. It also had the task of overcoming a major strike which nearly bankrupted the company back in the 1950s. It also had to cut staff and take out loans.
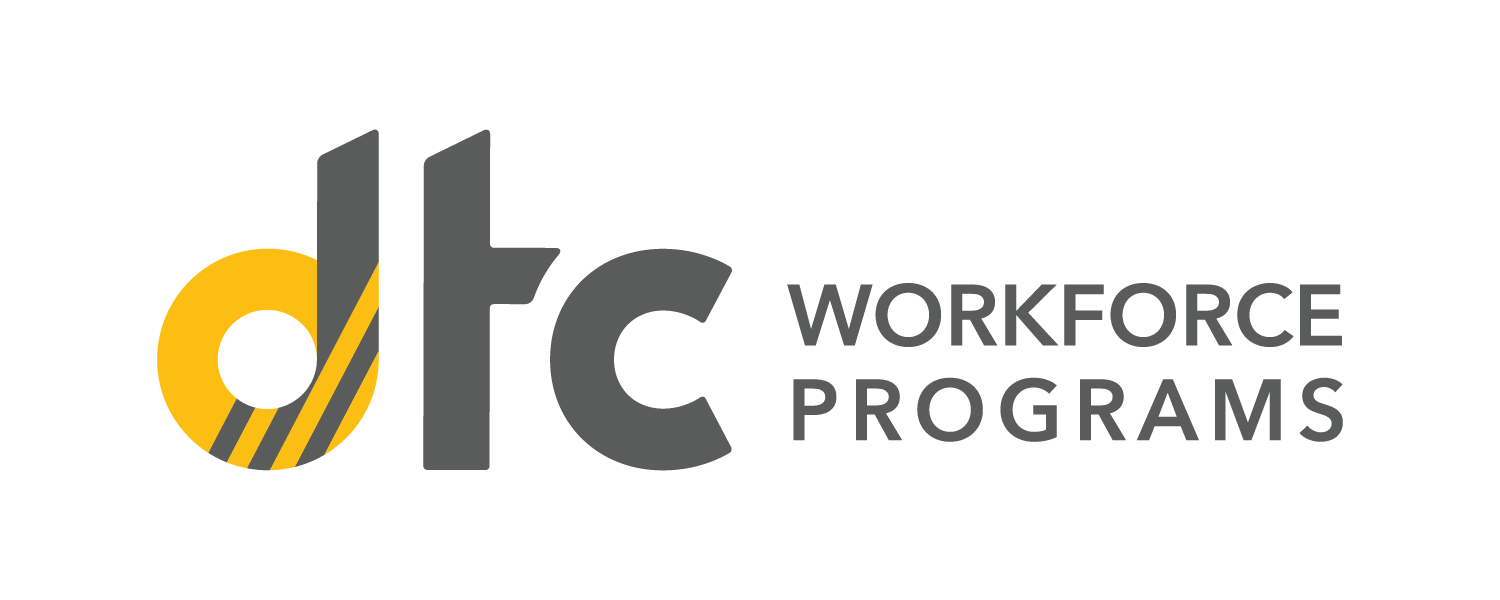
Toyota also established a "driving academy" to help people get their driver's licenses. The company also made a range of cars that are specifically designed for the U.S. marketplace. These initiatives helped it attract customers to its dealers.
Toyota's success in the automobile industry depends on its ability to innovate and create value. It is also dependent upon its ability build relationships with suppliers.
FAQ
What are the responsibilities of a production planner
Production planners ensure all aspects of the project are delivered within time and budget. They make sure that the product and services meet client expectations.
What does it take to run a logistics business?
You need to have a lot of knowledge and skills to manage a successful logistic business. You must have good communication skills to interact effectively with your clients and suppliers. You will need to know how to interpret data and draw conclusions. You need to be able work under pressure and manage stressful situations. To increase efficiency and creativity, you need to be creative. To motivate and guide your team towards reaching organizational goals, you must have strong leadership skills.
It is important to be organized and efficient in order to meet tight deadlines.
What are the responsibilities of a logistic manager?
A logistics manager makes sure that all goods are delivered on-time and in good condition. This is achieved by using their knowledge and experience with the products of the company. He/she should also ensure enough stock is available to meet demand.
What is the best way to learn about manufacturing?
The best way to learn about manufacturing is through hands-on experience. But if that is not possible you can always read books and watch educational videos.
Statistics
- According to a Statista study, U.S. businesses spent $1.63 trillion on logistics in 2019, moving goods from origin to end user through various supply chain network segments. (netsuite.com)
- You can multiply the result by 100 to get the total percent of monthly overhead. (investopedia.com)
- It's estimated that 10.8% of the U.S. GDP in 2020 was contributed to manufacturing. (investopedia.com)
- In the United States, for example, manufacturing makes up 15% of the economic output. (twi-global.com)
- In 2021, an estimated 12.1 million Americans work in the manufacturing sector.6 (investopedia.com)
External Links
How To
How to Use the Just-In-Time Method in Production
Just-in-time is a way to cut costs and increase efficiency in business processes. It is a process where you get the right amount of resources at the right moment when they are needed. This means that you only pay the amount you actually use. Frederick Taylor first coined this term while working in the early 1900s as a foreman. He saw how overtime was paid to workers for work that was delayed. He concluded that if workers were given enough time before they start work, productivity would increase.
JIT teaches you to plan ahead and prepare everything so you don’t waste time. Also, you should look at the whole project from start-to-finish and make sure you have the resources necessary to address any issues. You'll be prepared to handle any potential problems if you know in advance. You won't have to pay more for unnecessary items.
There are many types of JIT methods.
-
Demand-driven: This is a type of JIT where you order the parts/materials needed for your project regularly. This will allow you to track how much material you have left over after using it. This will allow you to calculate how long it will take to make more.
-
Inventory-based : You can stock the materials you need in advance. This allows you to predict how much you can expect to sell.
-
Project-driven: This means that you have enough money to pay for your project. You will be able to purchase the right amount of materials if you know what you need.
-
Resource-based JIT: This type of JIT is most commonly used. Here, you allocate certain resources based on demand. You will, for example, assign more staff to deal with large orders. If you don't receive many orders, then you'll assign fewer employees to handle the load.
-
Cost-based : This is similar in concept to resource-based. But here, you aren't concerned about how many people your company has but how much each individual costs.
-
Price-based pricing: This is similar in concept to cost-based but instead you look at how much each worker costs, it looks at the overall company's price.
-
Material-based: This approach is similar to cost-based. However, instead of looking at the total cost for the company, you look at how much you spend on average on raw materials.
-
Time-based: Another variation of resource-based JIT. Instead of worrying about how much each worker costs, you can focus on how long the project takes.
-
Quality-based JIT: Another variation on resource-based JIT. Instead of thinking about the cost of each employee or the time it takes to produce something, you focus on how good your product quality.
-
Value-based: This is one of the newest forms of JIT. You don't worry about whether the products work or if they meet customer expectations. Instead, you are focused on adding value to the marketplace.
-
Stock-based: This inventory-based approach focuses on how many items are being produced at any one time. This is used to increase production and minimize inventory.
-
Just-in-time planning (JIT): This is a combination JIT and supply-chain management. It's the process of scheduling delivery of components immediately after they are ordered. It reduces lead times and improves throughput.