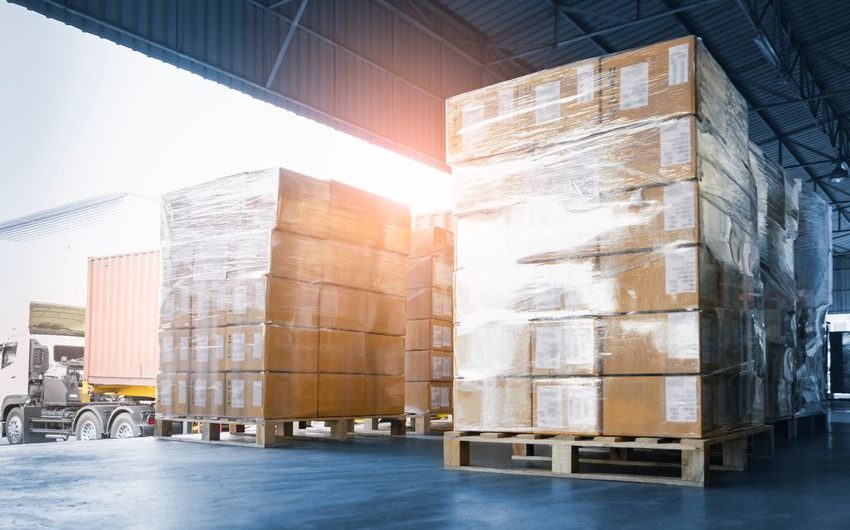
Toyota Motor Manufacturing Indiana Inc., located in Gibson County in Indiana, is the first Toyota plant that is wholly owned by Toyota. The plant produces Toyota's fullsize pickup trucks, such as the Avalon or the Corolla, and also the Sienna small van. It also produces Toyota's best-selling hybrid, the Toyota RAV4 Hybrid.
The plant was originally intended to make the Toyota Highlander. Instead, it moved to Gibson County, Indiana. Since 2011, the plant has produced Toyota's RAV4 Hybrid compact SUV, and Lexus ES 350. The plant was worth more than $1.33 Billion in 2017.
The plant also manufactures the Toyota Safety Sense 2.5+, which features automatic emergency braking. The plant also prepares all of the new 2018 Camry models. New features include a new transmission, greater power and a stylish design. It will cost $25,900
Toyota's Camry is the most popular car in America. It is America's best-selling midsize sedan, and it has been for over 15 years. Toyota has manufactured 10 million Camrys in Kentucky. This plant is the first to produce the hybrid model in North America.
Toyota Production System refers to a set of techniques and practices that improve quality and efficiency. This system includes 600 Toyota engineers. It also houses the Toyota Production Engineering and Manufacturing Center. The center will be the first to produce hydrogen fuel cell modules suitable for heavy-duty commercial trucks. The facility can build up to 100,000 vehicles per year.
Toyota has invested $1.5B in the plant over five years. It has also hired 700 additional workers. By 2020, this investment will provide 470,100 additional jobs in the United States. Toyota has made over $147 Million in Kentucky non-profit partners since 1986.
The Toyota Camry is a reliable and stylish vehicle. It comes with the GAK platform and a completely new transmission. It is also fun to drive. In July of this year, Consumer Reports highlighted the Toyota Camry as one of the best-selling cars in America.
The Toyota production system includes a number of elements, including continuous improvement, just-in-time parts delivery, and a sophisticated robotic welding system. The Toyota Production Engineering and Manufacturing Center is a good example of how Toyota has made the most of its investment in Kentucky.
Toyota has made significant savings on its production hall construction and air conditioning costs by using a new design. The Visitor Center has interactive video displays, and exhibits on hybrid technologies. Toyota will be producing up to 2,000,000 vehicles in North America over the next 10 year. This is the largest Toyota facility outside Japan.
Toyota's New Global Architecture is a big step in improving the company's production system. The strategy includes a brand new engine, a new organization of production and a module which unifies the vehicle components. While the new design is a reflection of Toyota's traditional values, it retains its innovative spirit.
FAQ
Why automate your warehouse?
Modern warehouses have become more dependent on automation. With the rise of ecommerce, there is a greater demand for faster delivery times as well as more efficient processes.
Warehouses must be able to quickly adapt to changing demands. To do so, they must invest heavily in technology. Automation of warehouses offers many benefits. These are some of the benefits that automation can bring to warehouses:
-
Increases throughput/productivity
-
Reduces errors
-
Increases accuracy
-
Safety is boosted
-
Eliminates bottlenecks
-
Companies can scale up more easily
-
It makes workers more efficient
-
It gives visibility to everything that happens inside the warehouse
-
Enhances customer experience
-
Improves employee satisfaction
-
Minimizes downtime and increases uptime
-
High quality products delivered on-time
-
Removes human error
-
This helps to ensure compliance with regulations
What are the 4 types manufacturing?
Manufacturing is the process that transforms raw materials into useful products. It can involve many activities like designing, manufacturing, testing packaging, shipping, selling and servicing.
How can manufacturing avoid production bottlenecks
Avoiding production bottlenecks is as simple as keeping all processes running smoothly, from the time an order is received until the product ships.
This includes planning for both capacity requirements and quality control measures.
Continuous improvement techniques like Six Sigma are the best way to achieve this.
Six Sigma Management System is a method to increase quality and reduce waste throughout your organization.
It's all about eliminating variation and creating consistency in work.
What jobs are available in logistics?
There are many jobs available in logistics. Some of them are:
-
Warehouse workers – They load, unload and transport pallets and trucks.
-
Transportation drivers – These drivers drive trucks and wagons to transport goods and pick up the goods.
-
Freight handlers - They sort and pack freight in warehouses.
-
Inventory managers: They are responsible for the inventory and management of warehouses.
-
Sales representatives - They sell products.
-
Logistics coordinators - They organize and plan logistics operations.
-
Purchasing agents are those who purchase goods and services for the company.
-
Customer service representatives – They answer emails and phone calls from customers.
-
Ship clerks - They issue bills and process shipping orders.
-
Order fillers: They fill orders based off what has been ordered and shipped.
-
Quality control inspectors: They inspect outgoing and incoming products for any defects.
-
Others - There are many other types of jobs available in logistics, such as transportation supervisors, cargo specialists, etc.
What is the importance of automation in manufacturing?
Automation is essential for both manufacturers and service providers. Automation allows them to deliver services quicker and more efficiently. It also helps to reduce costs and improve productivity.
Statistics
- [54][55] These are the top 50 countries by the total value of manufacturing output in US dollars for its noted year according to World Bank.[56] (en.wikipedia.org)
- Job #1 is delivering the ordered product according to specifications: color, size, brand, and quantity. (netsuite.com)
- You can multiply the result by 100 to get the total percent of monthly overhead. (investopedia.com)
- In 2021, an estimated 12.1 million Americans work in the manufacturing sector.6 (investopedia.com)
- According to a Statista study, U.S. businesses spent $1.63 trillion on logistics in 2019, moving goods from origin to end user through various supply chain network segments. (netsuite.com)
External Links
How To
How to use the Just In-Time Production Method
Just-intime (JIT), which is a method to minimize costs and maximize efficiency in business process, is one way. It is a process where you get the right amount of resources at the right moment when they are needed. This means that you only pay for what you actually use. Frederick Taylor first coined this term while working in the early 1900s as a foreman. He noticed that workers were often paid overtime when they had to work late. He decided to ensure workers have enough time to do their jobs before starting work to improve productivity.
JIT is about planning ahead. You should have all the necessary resources ready to go so that you don’t waste money. It is important to look at your entire project from beginning to end and ensure that you have enough resources to handle any issues that may arise. You will have the resources and people to solve any problems you anticipate. You won't have to pay more for unnecessary items.
There are different types of JIT methods:
-
Demand-driven: This is a type of JIT where you order the parts/materials needed for your project regularly. This will allow you to track how much material you have left over after using it. This will let you know how long it will be to produce more.
-
Inventory-based: This is a type where you stock the materials required for your projects in advance. This allows one to predict how much they will sell.
-
Project-driven: This is an approach where you set aside enough funds to cover the cost of your project. If you know the amount you require, you can buy the materials you need.
-
Resource-based: This is the most common form of JIT. This is where you assign resources based upon demand. If you have many orders, you will assign more people to manage them. You'll have fewer orders if you have fewer.
-
Cost-based: This is similar to resource-based, except that here you're not just concerned about how many people you have but how much each person costs.
-
Price-based: This is similar to cost-based but instead of looking at individual workers' salaries, you look at the total company price.
-
Material-based: This approach is similar to cost-based. However, instead of looking at the total cost for the company, you look at how much you spend on average on raw materials.
-
Time-based JIT is another form of resource-based JIT. Instead of focusing solely on the amount each employee costs, focus on how long it takes for the project to be completed.
-
Quality-based JIT - This is another form of resource-based JIT. Instead of thinking about how much each employee costs or how long it takes to manufacture something, you think about how good the quality of your product is.
-
Value-based JIT : This is the newest type of JIT. In this case, you're not concerned with how well the products perform or whether they meet customer expectations. Instead, you are focused on adding value to the marketplace.
-
Stock-based: This inventory-based approach focuses on how many items are being produced at any one time. This is used to increase production and minimize inventory.
-
Just-in-time (JIT) planning: This is a combination of JIT and supply chain management. It's the process of scheduling delivery of components immediately after they are ordered. It reduces lead times and improves throughput.